Refurbish Or Replace: The Inside Scoop For Walk-In Coolers And Freezers
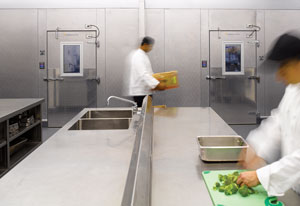
Manufacturers estimate the average lifespan of a walk-in cooler or freezer to be about 15 years. However, with decent care and maintenance, they can last well beyond that. Sometimes all it takes is a little refurbishment.
Let’s face it, employees can be hard on equipment, and walk-ins are no exception. They slam doors and jimmy closers, yank the handles, ram the interior and exterior walls and door with carts and pallet trucks, buckle the floor with heavy loads, knock into the evaporator unit; walk-ins can suffer a lot of abuse. At some point, you might want to weigh the cost of refurbishing your walk-in against the cost of outright replacement. Many manufacturers offer replacements for the most commonly worn components, including walls, floors, doors and refrigeration systems. One spokesperson estimates that, done right, refurbishing a worn walk-in unit can add another five to seven years to its lifespan.
The call for refurbishing walk-ins—vs. installing new—really gained traction about 10 years ago when the Great Recession was just coming on, according to several manufacturers. Operators had to put major capital expenditures on hold and make-do with existing equipment as much as possible. One estimate puts the cost of a typical walk-in refurbishment at a third of the cost of installing a new unit.
What makes a walk-in a good candidate for refurbishment? “If the box is sound, it still holds temperature, has no water infiltration into the insulation and no air leaks, refurbishment can make sense,” one manufacturer told us.
Where’s The Wear And Tear?
Doors, including hinges, floors, walls and refrigeration systems take the most abuse. Depending on the condition of the rest of the unit, replacing any of these specific components may be enough to keep your existing unit in service for years more.
According to manufacturers, doors are one of the components that need replacing most often. “The unit’s interior and refrigeration system may be just fine, and all it takes to keep it functioning properly is a new door that maintains the seal,” says a manufacturers’ rep.
He estimates that a simple door-for-door replacement could take only a couple of hours. Some manufacturers offer replacement doors only for their own brand of walk-ins, while others offer new doors for any brand. Replacement doors for different brands sometime cover the existing door frame and mount to the walk-in’s outer surface. More complicated replacements may take a little more time to complete.
One manufacturer suggests that to extend the life of any door, new or original, it’s smart to include a stainless kickplate in the specification.
Floors are the high-traffic areas, and they’ll show excessive wear before other walk-in areas. Most manufacturers offer a variety of flooring, each designed to handle different weight loads. If canvassed, most employees don’t know that weight limit or even if they did, they don’t know the weight of the loads they’re stocking. A walk-in cooler installed with a flooring system designed for lighter loads is going to buckle and dent if employees use carts to transport beer kegs and then drop them on the floor, for example. Overloaded shelving might buckle the floor, separating the surface from its insulating foam. If employees spill liquids and don’t clean them up quickly, they can seep into flooring seams, again separating flooring from foam.
Typically, you have two options for repairing the floor: remove and replace the original or lay a new floor over the old.
Damage happens less frequently to walls than it does to doors and floors, manufacturers tell us, but it does happen and should be monitored. Some employees can overshoot, ramming walls with cart corners or pallet lifts, punching holes in walls or buckling seams. Bumper rails can help avoid the abuse, but they take up room around the walk-in perimeter. Stainless diamond-pattern wall finishes are another line of defense, but you have to weigh upfront expense with the additional years of walk-in use that protection buys you. Some stored items, including acidic vegetables or salty seafood, can corrode wall panels. Wall repairs are pretty easy to make, according to sources. Sometimes it’s not even necessary to move product from the walk-in during the process.
Refrigeration System Replacement
Like the walk-in boxes themselves, the refrigeration systems that provide the low temperatures inside last on average 15 years with the potential for many more, says one manufacturer. Like doors, floors and walls, these systems are replaceable without requiring the installation of an entire walk-in unit. One manufacturer says that a unit in need of both structural and refrigeration repairs, however, is probably a good candidate for total replacement.
When refrigeration systems aren’t working, several components could be culprits. Condenser coils can take about four hours to replace. Evaporators, located inside the walk-ins are subject to the same corrosion from foods as the walk-in interior; all of that acidity and salt gets sucked through the evaporator coils. An evaporator can take a couple of hours to replace.
Failed fan motors may only require a half-hour to replace. Even replacing an entire refrigeration system (generally installed on top of a walk-in unit) may only take a few hours. Remote systems may take longer, but location and how easy it is for servicers to get to the system play a role in replacement time.
If you can keep the doors to the cooler or freezer closed during a repair, chances are you won’t have to move product out to temporary cold storage—but you have to monitor temperatures throughout the repair process. (See sidebar "Prep For Repair.")
Who To Call?
When weighing the choice between refurbishing and replacing your walk-in cooler or freezer, it’s best to call the manufacturer first. Be aware that some manufacturers offer refurbishing services, others do not. And even among those who do, they don’t necessarily do the refurbishing work, but contract the work out to other professionals instead. Still, it’s best to start with the manufacturer first and follow through from there with their guidance.
Prep For Repair
Repair times for your walk-in cooler or freezer range from an hour or two to a couple days. Before beginning any work, discuss the need for temporary storage for the food in your unit with the manufacturer or service company doing the repair. Faster repairs, such as replacing a fan motor in your refrigeration system, can be done without removing any food. Keeping the door closed keeps out warmer exterior air and should keep the temperature at the proper level inside. Still, make sure to schedule repairs during off-hours or during slow periods as trips to the unit for product will affect interior temperatures.
For longer repair jobs, some manufacturers and service companies offer short-term cooler and freezer rentals. At least one manufacturer offers turnkey repair services including temporary storage. Your food purveyor may also have refrigerated trucks for rental. One final tip: If you’re emptying the walk-in for repair, use the opportunity to also give the walk-in a thorough cleaning.
- Advertisement -
- Advertisement -
TRENDING NOW
- Advertisement -
- Advertisement -
- Advertisement -