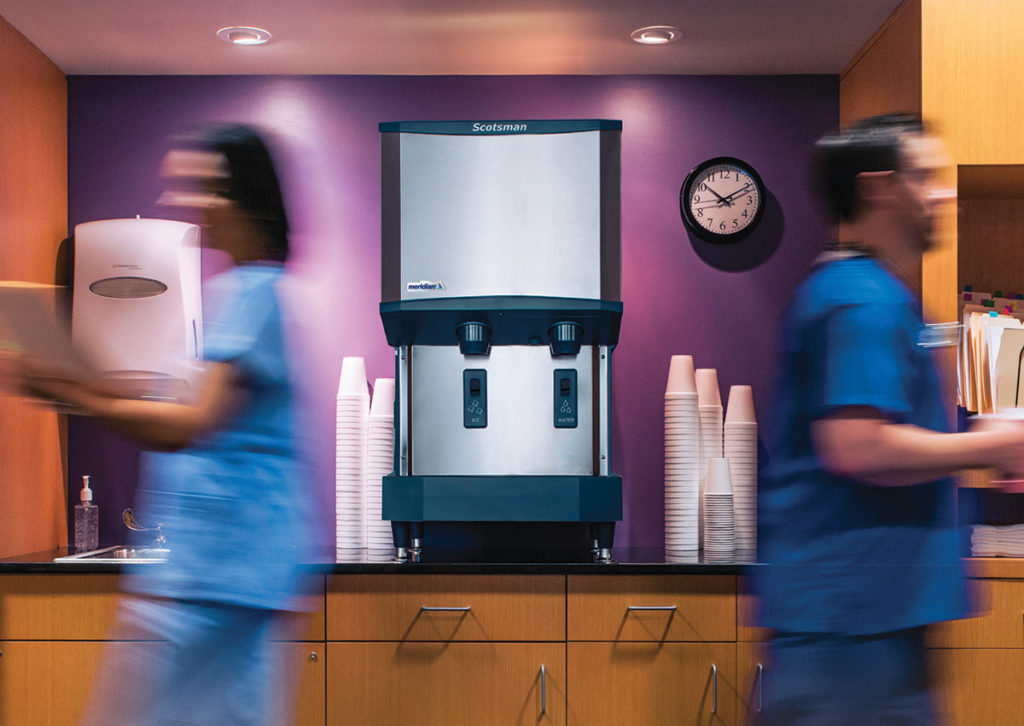
Providing ice and water in healthcare settings is challenging on many levels. Determining how to supply enough is important, but keeping it safe can be a matter of life and death. Fortunately, manufacturers know both the advantages and dangers of supplying ice and water and update dispensers all the time to make them safer and more reliable. Here are top tips from several manufacturers to help you when you’re shopping for ice-and-water dispensers.
Cold Nuggets
Not all ice is the same. Many machines create ice cubes, which can be delivered in whole, half or crushed form. But most of the machines in healthcare facilities produce nugget ice, also called compressed flake ice. This is not the same as crushed ice. Nugget ice is softer than ice cubes and still contains some liquid water.
Nugget ice has many advantages, including being more chewable than regular ice. In situations where water intake is limited, as is common with dialysis patients, chewing ice is often the only option they are allowed. Nugget ice presents less of a choking hazard than cubes, and it also is easier on the teeth. It also is better for filling ice bags and ice packs.
The hardness of the nuggets is generally identified by the amount of liquid water, typically between 5% to 20%. (Regular ice cubes are close to 100% ice.) In addition to hardness, nuggets also are defined by size. So, you can get the softness and size you need (though the smaller and softer the ice is, the harder it is to dispense). The dispenser clearance is another thing to keep in mind: will you be filling cups or pitchers? At least one manufacturer offers an 11½-in. dispenser clearance to make it easy to fill taller containers.
Sensor Or No Sensor
Among the more popular advances being introduced for dispensers in healthcare settings is the infrared optical sensor, which makes touch-free dispensing possible. This feature recognizes when a receptacle is placed in front of the dispenser and triggers the release of ice. Obviously, the less equipment is touched, the fewer germs are spread. However, the optical sensor also adds another level of complexity and additional cost, so push-button dispensers still outsell the optical devices. However, in situations where sanitation is of paramount importance, this gives healthcare facilities an additional level of protection.
Keeping Up With Upkeep
A lot of advances in recent years revolve around making it easier to clean and maintain dispensers. Stainless is a common choice for the exteriors of these machines, because it’s easy to clean. Removable front panels give quick access to the working parts inside.
More than one manufacturer mentioned that air filters help keep machines cleaner and extend their lives, but they need to be changed out regularly or they’re ineffectual. Others identified maintenance-free bearings’ role in reducing maintenance requirements: augur bearings on these machines are sealed and do not need to be greased during regular maintenance.
Another vendor related that machines have been re-engineered to eliminate places water might collect (and develop mold). Adding antimicrobial properties to key components contributes to the fight against bacteria. In one dispenser, a self-flushing cycle regularly clears standing water, so that the water coming out of the machine is always fresh. Because of their concern about biofilms, manufacturers have all built in multiple ways to keep the machines clean. One manufacturer pointed out that, because biofilms can grow on spouts, their model’s spout can twist off and be cleaned.
There’s always some complexity in maintaining dispensers, which is why deep cleaning is best left to qualified technicians, but design advances have cut down on difficulty and time needed for the task. One manufacturer detailed a semi-automatic cleaning function. The technician takes off the front panel, puts cleaner/sanitizer in a cup, and the machine cleans everything then flushes out the sanitizer. Others described internal diagnostics, to minimize downtime, while another relates that its machines have a QR code inside, which includes maintenance instructions. “We still send a manual, but QR codes, which can be scanned with a smartphone, are faster. We are bringing in more technology, but we’re trying to make it intuitive as much as possible.”
Capacity Questions
A major caveat when figuring out capacity is to not think in terms of production alone. In addition to keeping in mind how much a machine makes, you also have to think about how much it can store. For example, a dispenser may be able to produce 425 lb. of ice in one day but only have space to store 12 lb. at a time. Dispensers only make ice when their hoppers start to get empty, so you have to think in terms of how much you will need during peak demand periods. You’ll want more storage if you have periods when demand spikes.
Storage capacities can range from 12 lb. to 400 lb. If you get too large a capacity, it’s not efficient. If you get a machine that’s too small, it’s not useful. That said, one manufacturer suggests also considering whether future need might increase, in which case, you don’t necessarily want to get the minimum you need.
Calculating how much ice you need will vary by location, but manufacturers offer some guidelines for deciding what you need. One manufacturer suggests figuring about 1 lb. of ice per person per day for ice/water dispensers in the hospital cafeteria. On the patient floor, however, one calculates by bed: about 10 lb. per bed per day. This takes into account not only the patient, but also nurses, visitors, and draws for such items as ice packs, for example. Other manufacturers suggest 2 to 3 lb. per employee or 7 lb. per bed.
Fitting In
Capacity is important, but you want to make sure the machine you order fits the space you have. Often, nursing stations are limited in size, so bigger is not always better. Sometimes, two smaller machines more widely distributed would be better than one big machine. Also, a dispenser can’t be wedged into a tight space. There must be room on the sides and top for air vents to dispel heat. You also don’t want to put one where air from ventilation ducts will blow across it, as the air often carries dust and bacteria. Also avoid placing units directly next to a food-preparation zone; food particles can become a source of biofilm growth.
One manufacturer points out that, because its dispensers are 31-in. high, you can’t have cabinets above them. Manufacturers usually offer stands, thereby making countertop dispensers into floor models, because sometimes there is no available counter space. This makes positioning less limited, but you’ll need the floor space.
Noise is another issue. Ice-and-water dispensers shouldn’t be set too close to a work area, as the machine’s blowers can be distracting and compressors make noise. But it’s not always possible to position a device where no one will hear it. One manufacturer has developed a system where the compressor doesn’t restart when demand is lower, as is generally the case at night. This makes it more likely that nearby patients will sleep better. Another manufacturer notes that they have upgraded condensers and fans, to make their machines quieter. “They’ll never be 100% silent, but we’re trying to improve the patient experience.”
A final consideration is meeting energy goals. One manufacturer noted that its current machines are 25% more energy efficient than previous models. Check that the machine you pick meets whatever energy guidelines are enforced at your location.
What About Water?
A water source will be part of finding a place for your dispenser, but there also must be a drain. You can’t have a drainless ice/water dispenser in a healthcare setting. Standing water gives germs an easy place to multiply.
In addition, consider the quality of water you will use. If you have hard water, minerals in the water can clog your dispenser. Your options include softening the water, having a regular descaling program, or looking for a dispenser with an automatic descaling function.
How you treat the water also can be an issue from the patient point of view. One manufacturer pointed out that hospitals have to decide between using a carbon filter, which gives them water that tastes good, or not using the carbon, which leaves the chlorine. Chlorine in the water reduces germs and helps inhibit mold growth in ice maker parts, but doesn’t taste as good. And poor-tasting water can lead to lower patient satisfaction scores.
Moving Forward
All manufacturers had an appreciation for the part their machines play in the healthcare environment, along with a desire to have a positive impact on patients, visitors, and healthcare providers. Because of that, even though currently available dispensers are remarkably advanced (see the latest models throughout this story), manufacturers want to keep improving safety, performance, and ease of maintenance. As one manufacturer notes, “We’re already looking at making more improvements. Next year will see new features.”
Click to the next page for the Ice-And-Water Dispenser Gallery.
RELATED CONTENT
- Advertisement -
- Advertisement -
- Advertisement -
TRENDING NOW
- Advertisement -
- Advertisement -
- Advertisement -