From the Editor: Good Work
One service technician is on a mission to bring more talent to the industry.
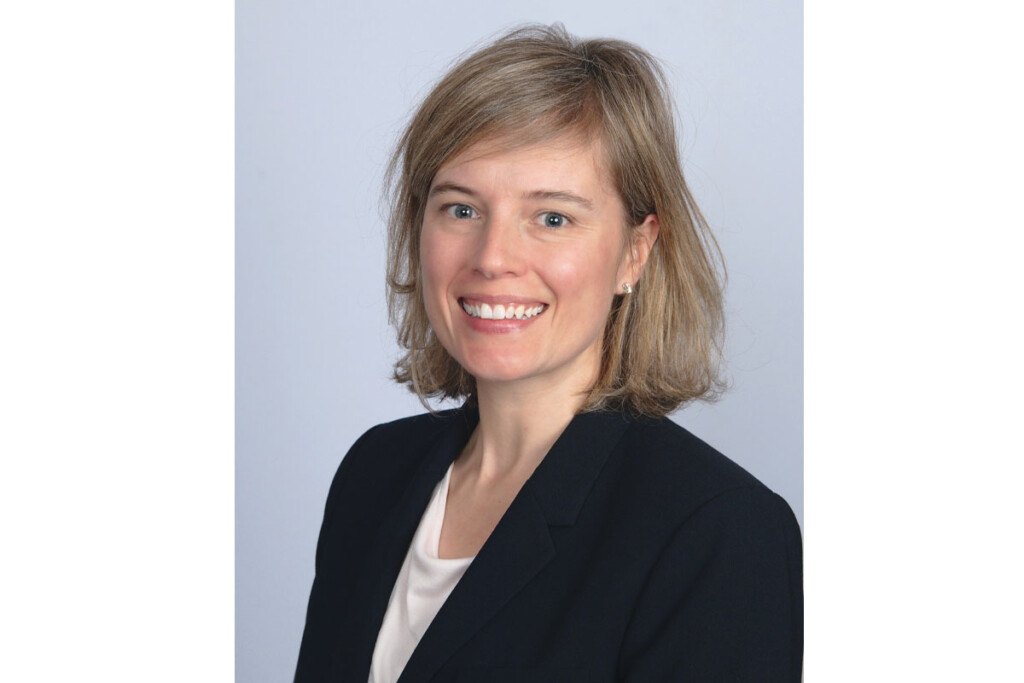
Finding good talent is tough and one person on the service side getting the work done is Zac Hampton.
Hampton serves as a senior technician and trainer at Auston Mealer’s Restaurant Equipment Service, based in Dyersburg, Tenn. He’s also a member of CFESA’s Young Professionals Committee. I had the chance to meet him when we served on a panel together at CFESA’s Region 3 Meeting this spring. Doug Becker, regional manager, General Parts, and Manuel Griego, owner, Arrowhead Superior Refrigeration Service, also joined us as panelists.
Hampton’s efforts to recruit talent ranges from the simple act of wearing a YPC badge in the field to setting up booths at high school and trade school career fairs. “People walk up and say, ‘What is YPC?’ and it gives me a chance to explain it and tell them what my job is about and the need for young people to come into this field,” Hampton says about the badge.
One thing he’s noticed lately with career fairs is the need to reach kids before they enter high school. “We’re going to start visiting more middle schools so we can put the idea (of this profession) in their heads a little earlier,” he says. “That way they have something to think about while they’re in high school, choosing their classes.”
Training marks a big part of retention, and it’s one of Hampton’s passions. He provides training to Auston Mealer’s technicians while in the field and at the company’s 26-seat classroom, complete with a smart board. Here, students have the opportunity to earn credit hours toward their apprenticeship. They receive manufacturer training as well. Additionally, Auston Mealer’s offers a family-like atmosphere, employing about 30 people total, plus competitive benefits.
Much like Hampton and others on the service side, the dealer community is investing in the next wave of talent, all to serve operators. See the FER 2025 Top Dealers Report. And stay tuned for the FER July/August issue, which will spotlight emerging leaders in the industry. I like to think of it as FER doing its part to keep this industry thriving with fresh talent.
ALLISON REZENDES
Editor-in-Chief
arezendes@fermag.com
3 THINGS
THREE TIPS WHEN WORKING WITH SERVICE AGENTS
Zac Hampton of Auston Mealer’s Restaurant Equipment Service offers the following advice to operators when it comes to working with technicians:
ASK FOR HELP
“I tell all my customers to call me when they need to buy a piece of equipment,” Hampton says. “I’ll help them choose what’s going to be productive for them, what’s not going to give them problems.”
MAKE A PLAN
Hampton pushes planned maintenance. “It extends the life of the machine,” he says. For example, operators who install an ice machine will want to set up a PM program on it just as they would a water filtration system.
GIVE LOTS OF DETAILS
The more an operator can share about an issue when they make a service call, the better chance for a first-time fix. For example, if a technician knows the equipment is under warranty, they can arrive with the appropriate tote filled with the most common parts.
RELATED CONTENT
- Advertisement -
- Advertisement -
- Advertisement -
TRENDING NOW
- Advertisement -
- Advertisement -
- Advertisement -